Автогонки — один из самых быстрых и технически продвинутых видов спорта, а связанные с ним производственные технологии находятся на переднем крае инноваций. двигателей гоночных автомобилей.
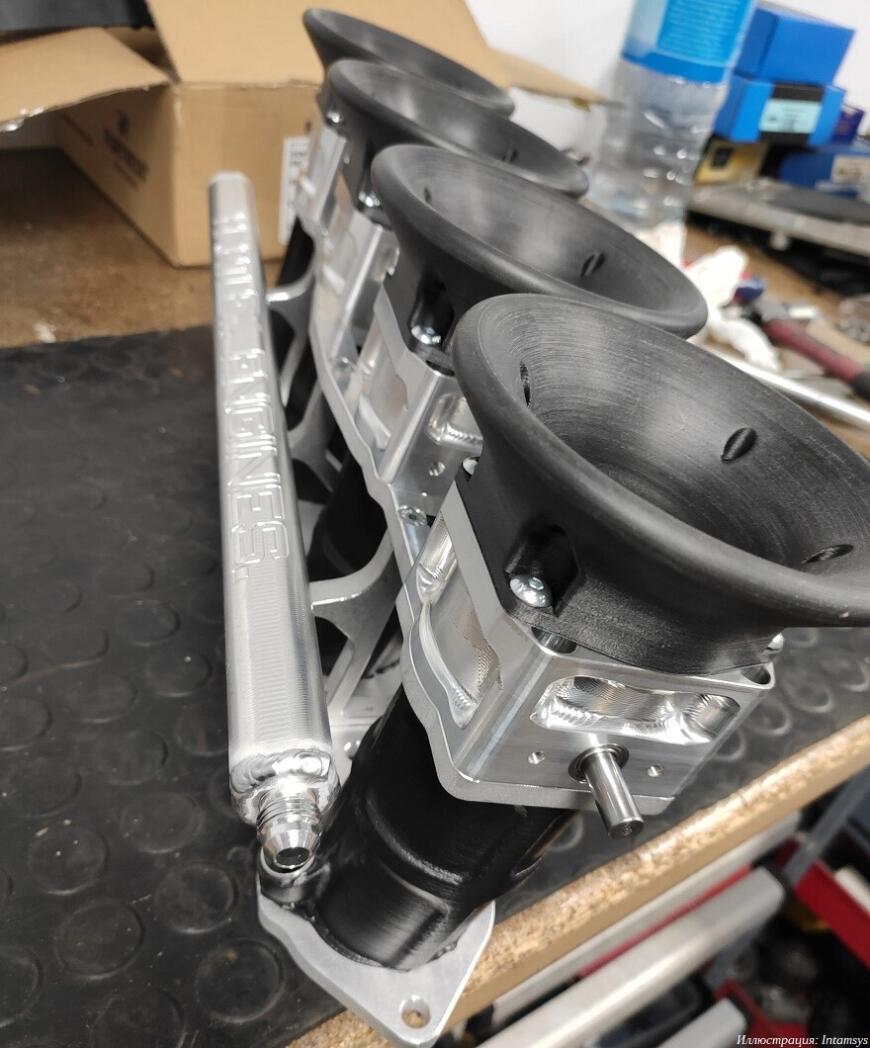
Новозеландская компания Hartley Engines and Motorsport занимается конструированием и производством двигателей и других компонентов для гоночных команд и небольших автопроизводителей. На счету клиентов этого предприятия многочисленные победы в чемпионатах Новой Зеландии и Австралии, рекорды скорости на соляном озере Бонневиль в заездах на машинах с однолитровыми двигателями, а также множество наград за инновации в мотоспорте. Флагманские силовые установки включают восьми- и двенадцатицилиндровые моторы мощностью свыше тысячи лошадиных сил, вдохновленные Формулой-1.
Ранее компания занималась в основном производством двигателей для ведущих гоночных команд, при этом основная часть работ велась в строгом секрете и только для избранных клиентов. Недавно предприятие расширило сферу деятельности поставками комплектов двигателей и передачей компетенций другим разработчикам, а также продажей комплектующих на открытом рынке.
«Мы осознали, что не можем и не хотим создавать двигатели для каждого соревнующегося — у нас просто не хватит времени. Для всех будет больше пользы, если мы откроем доступ к нашим компонентам и наработкам», — поясняет владелец компании Нельсон Хартли.
Одна из сильных сторон компании в том, что она способна очень быстро разрабатывать продукты и разворачивать производство. Парк предприятия включает токарные и пятиосевые фрезерные станки с ЧПУ, моторные динамометры и даже оборудование для аэродинамической продувки. Уже несколько лет Нельсон и его команда оттачивают гибридную методику производства двигателей с использованием комбинации фрезерованных, углепластиковых и 3D-печатных деталей. Один из примеров — переделка дроссельных заслонок с использованием 3D-печатных воздухозаборников и коллекторов.
«С самого начала мне был очевиден ряд серьезных преимуществ 3D-печати. Свойства некоторых продвинутых полимеров очень впечатляют и идеально подходят для таких вещей, как впускные коллекторы и другие компоненты. При 3D-печати впускных коллекторов мы используем высокотемпературный нейлон с 25-процентным содержанием углеродного волокна (PA-CF). Он лучше справляется с температурой, чем алюминий, так как проводит тепло очень медленно, оставляя забираемый воздух холодным и тем самым повышая эффективность сгорания. Дополнительный плюс 3D-печати коллекторов и воздухозаборников — гибкость дизайна. Мы очень серьезно относимся к форме впускного тракта. Это не просто отверстие в пластине: благодаря 3D-печати мы имеем возможность воспроизводить сложные изгибы и формы по CAD-моделям головок цилиндров».
Помимо 3D-печати готовых изделий предприятие полагается и на аддитивное производство формовочной оснастки, как в случае с углепластиковой нагнетательной камерой на иллюстрации ниже. Наладить 3D-печать высокотемпературными полимерами удалось не сразу: до ввода в эксплуатацию 3D-принтера Intamsys Funmat HT с термостатированной камерой доля брака достигала 80%.
«Мы выбрасывали больше распечаток, чем могли себе позволить: при цене расходников до пятисот долларов за килограмм, плюс доставка в Новую Зеландию, стоял вопрос рентабельности 3D-печати. После того как мы получили наш первый Intamsys Funmat HT, доля брака сократилась до пяти процентов! Многие в отрасли говорили, что мы не сможем делать серийные детали на 3D-принтере, но оборудование от Intamsys доказало, что это не так», — рассказывает Нельсон.
Обкатав первый Intamsys Funmat HT, компания купила второй такой же 3D-принтер, а теперь планирует приобрести еще четыре для нового, специализированного отдела аддитивного производства.
«Наш Intamsys Funmat HT обошелся всего в одну тридцатую стоимости пятиосевого обрабатывающего центра, но детали, которые мы на нем печатаем, имеют такую же ценность для клиентов. Поэтому, даже если 3D-печать в пересчете на деталь занимает больше времени, я могу позволить себе серийное производство на нескольких 3D-принтерах одновременно. В некоторых случаях это более эффективно, чем установка дополнительных станков с ЧПУ. Окупаемость инвестиций в аддитивные технологии оказалась чрезвычайно высокой. Раньше мы тратили часы на настройку станков и изготовление оснастки только для того, чтобы обработать или изготовить одну деталь. Теперь все, что мне нужно сделать, это нагреть Intamsys Funmat HT и нажать кнопку «Пуск». Никакая оснастка не требуется. Любой, кто говорит, что 3D-принтеры заменят все станки с ЧПУ, лжет, но точно так же недальновиден тот, кто говорит, что нельзя выполнять производственные работы на экономичном 3D-принтере», — заключает Нельсон.
>>>БАЗЫ ДАННЫХ(EMAIL, ТЕЛЕФОНЫ). БЕСПЛАТНО.<<<
Добавить комментарий
Для отправки комментария вам необходимо авторизоваться.