Компания General Electric планирует использовать строительный 3D-принтер высотой с трехэтажное здание для 3D-печати железобетонных секций ветрогенераторных башен.
Проект развивается уже пару лет, но финальной отработкой процесса займется недавно открывшийся центр в городе Бергене, штат Нью-Йорк, при поддержке Министерства энергетики США, вложившего в исследовательский проект пять миллионов долларов. Команда из двадцати человек проведет необходимые испытания с расчетом на промышленное внедрение через пять лет. Помимо GE в проекте участвуют швейцарский производитель строительных материалов Holcim и датская компания COBOD. Последняя предоставила необходимое аддитивное оборудование.
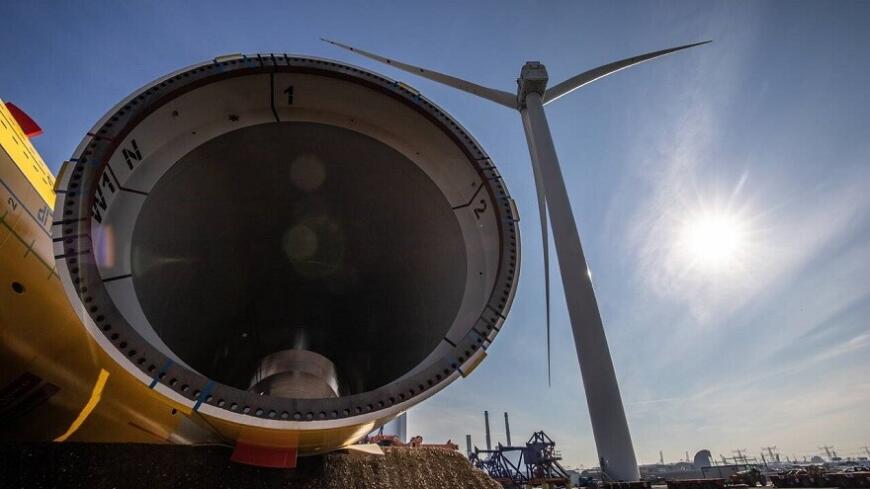
Строительные 3D-принтеры от СOBOD вообще-то имеют российские корни. Первой системой этой предприятия под обозначением BOD1 был по сути ребрендированный 3D-принтер ярославской компании «АМТ-Спецавиа», сотрудничавшей с датским стартапом на раннем этапе его существования. Сейчас COBOD работает самостоятельно, предлагая масштабируемые строительные аддитивные системы BOD2.
«Мы гордимся тем, что смогли предоставить этому центру новый тип 3D-принтера для печати бетоном — самый большой в мире. Наш 3D-принтер не имеет равных: он не только способен укладывать до десяти тонн настоящего бетона в час, но еще и первый строительный 3D-принтер с двойной осью X. C учетом многофункциональности этого 3D-принтера его можно считать скорее многофункциональным строительным роботом», — заявил основатель и генеральный директор COBOD Хенрик Лунд-Нильсен, совершенно запутав редакцию 3Dtoday.
Зачем все это нужно? Дело в трубах. Типичные башни ветрогенераторов — сварные конструкции из стальных труб. Сборка осуществляется на месте. Чем мощнее генератор, тем выше и толще башня, но упомянутые трубы надо как-то доставить на место, а у транспорта и дорог есть свои ограничения. Практический предел сейчас — трубы диаметром около четырех метров. С лопастями, кстати, была та же проблема, только в плане длины, но GE решила этот вопрос составными конструкциями.
Проблему с башнями корпорация надеется решить с помощью аддитивных технологий. Заниматься локализованным трубопрокатом в местах возведения ветрогенерирующих ферм — это пока совсем из области фантастики, а вот бетонные основания большого диаметра вполне можно печатать и армировать на месте с помощью разборного, транспортабельного 3D-принтера и команды сварщиков. Испытуемая система будет выращивать железобетонные секции общей высотой до двадцати метров.
Далее башни будут наращиваться с помощью привычных металлоконструкций до высоты порядка ста сорока метров. Это далеко не рекорд, но из-за описанных выше ограничений остается масса мест, где можно было бы строить эффективные фермы, если бы особенности транспортной инфраструктуры или ландшафта не мешали доставке негабаритных грузов и возведению стандартных конструкций. В любом случае, скорость и стабильность ветра увеличиваются с высотой, так что чем выше башня, тем выше эффективность генератора в целом.
Параллельно планируется исследовать возможность локального производства расходных материалов, хотя бы частичного. В центре будут использоваться как стандартные смеси, так и варианты с использованием местного песка и камня. В долгосрочной перспективе это поможет дополнительно сэкономить на логистике. Первые тесты будут проведены в цеховых условиях, а со следующего года команда приступит к испытаниям под открытым небом
>>>БАЗЫ ДАННЫХ(EMAIL, ТЕЛЕФОНЫ). БЕСПЛАТНО.<<<
Добавить комментарий
Для отправки комментария вам необходимо авторизоваться.